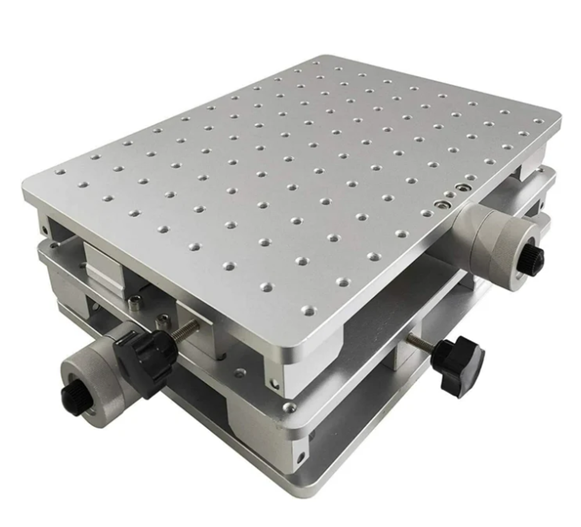
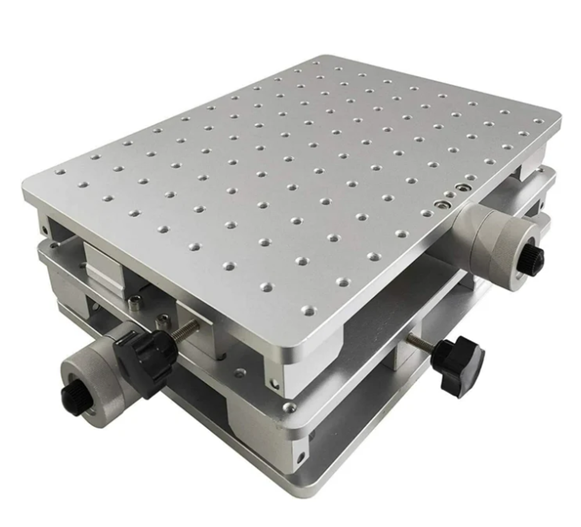
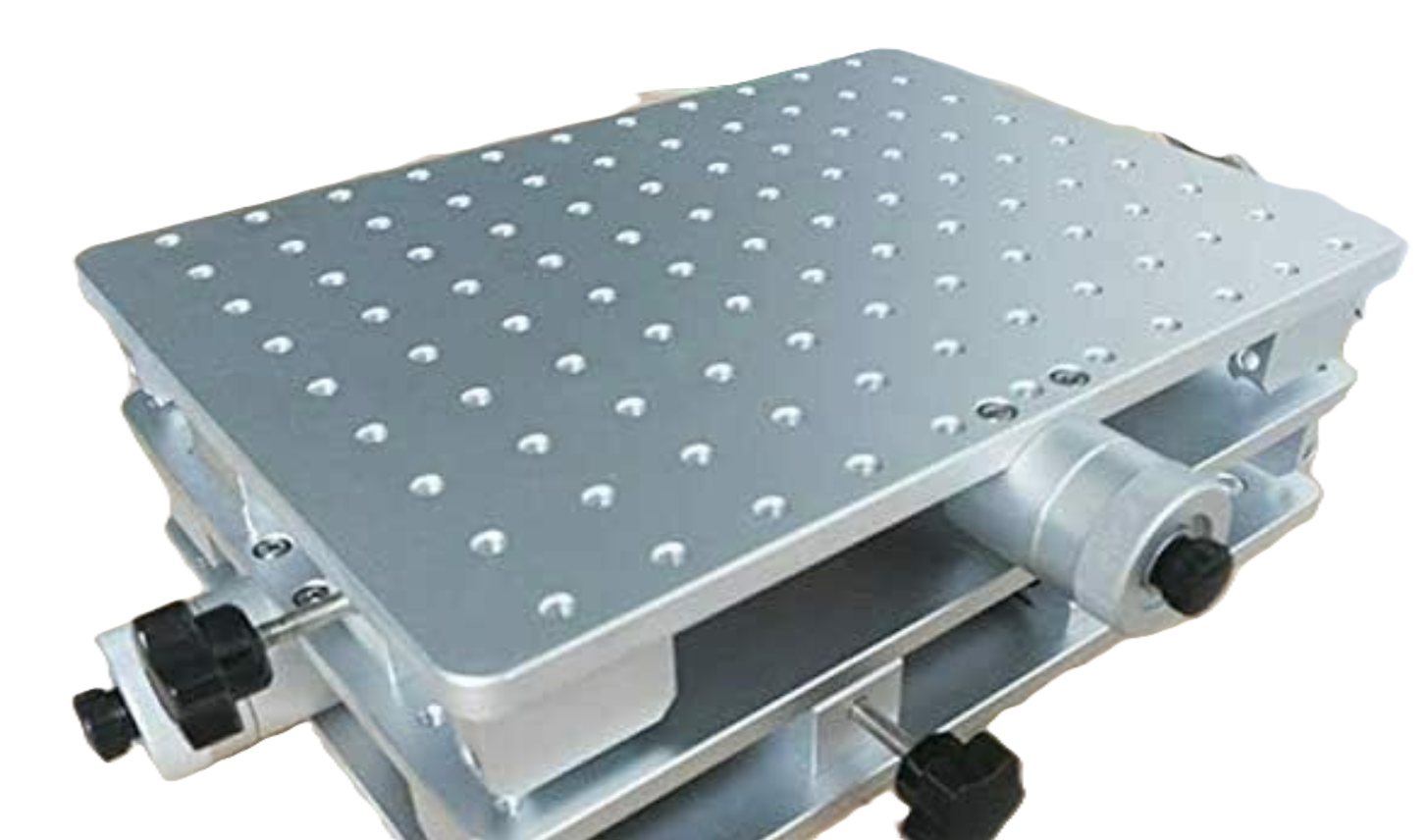
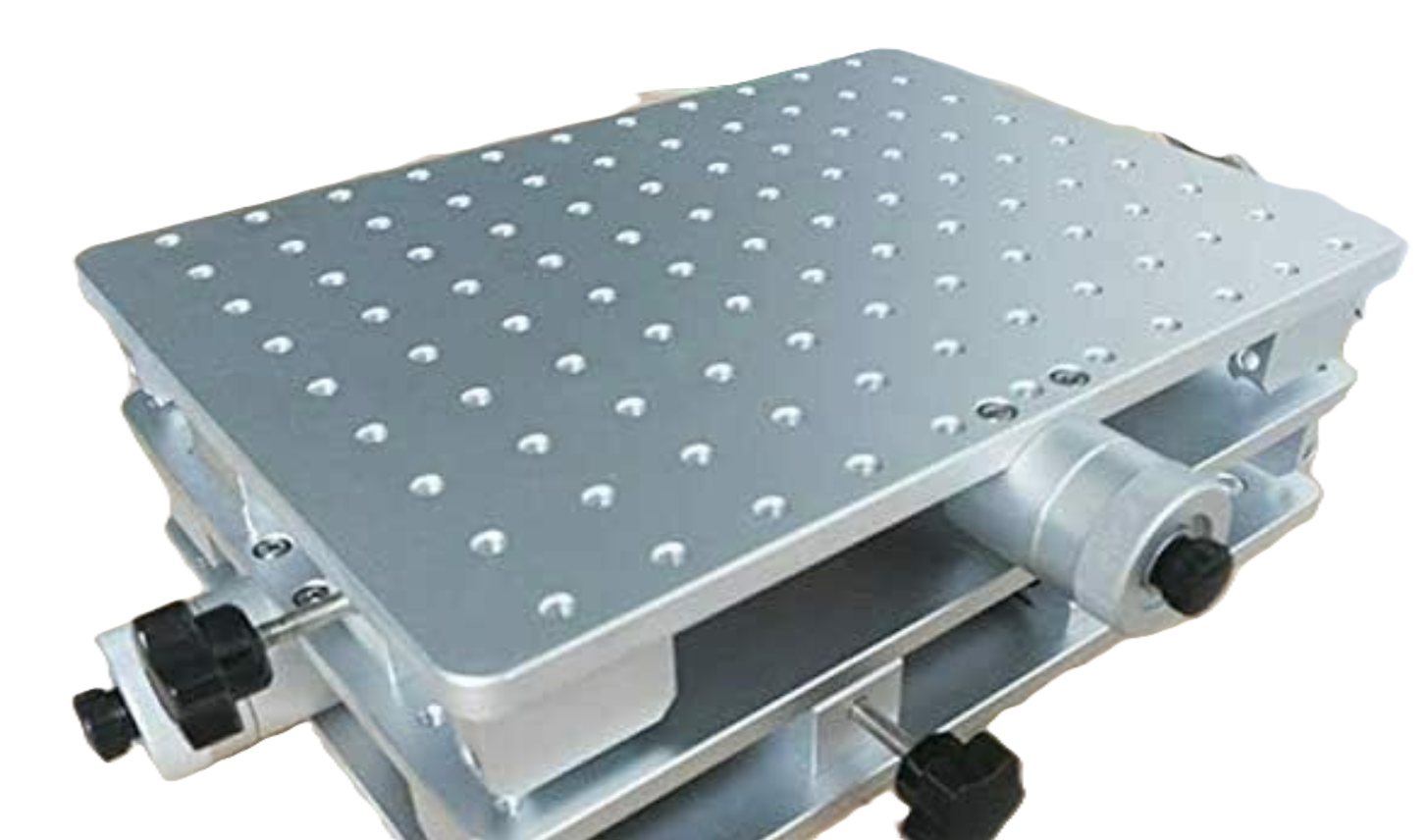
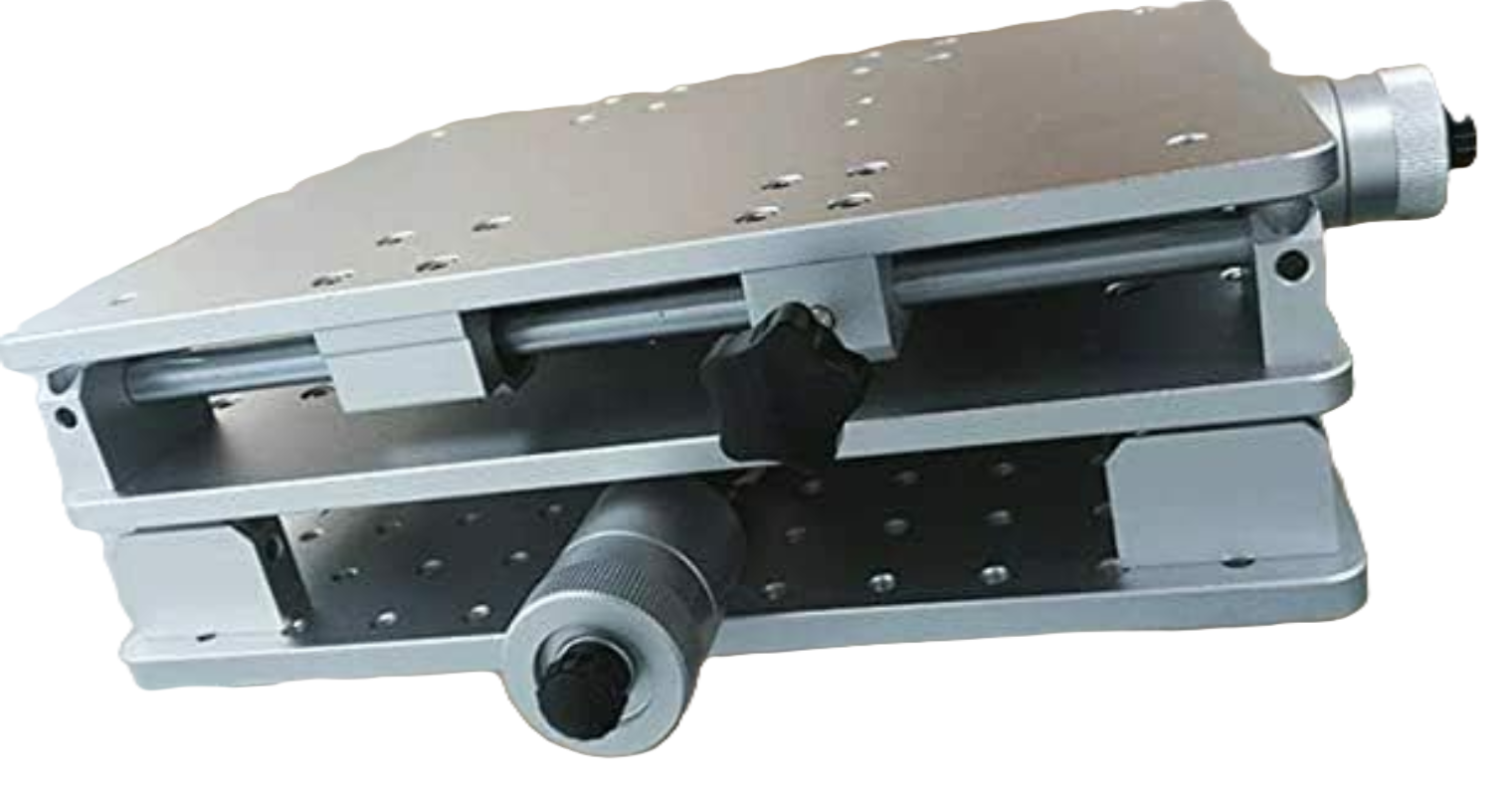
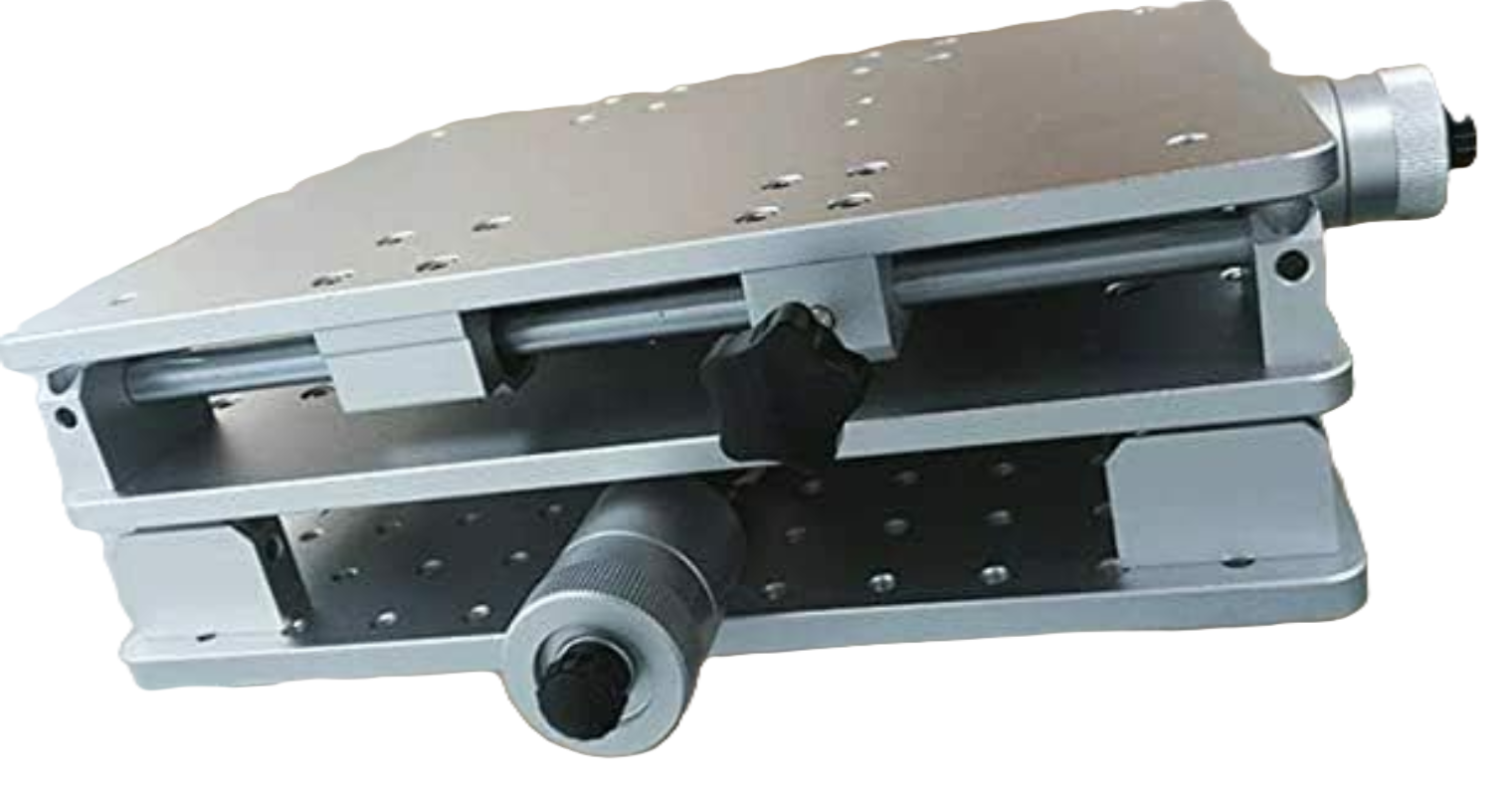
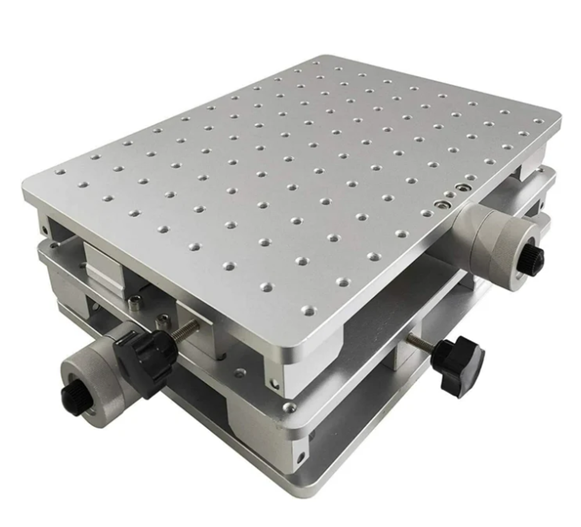
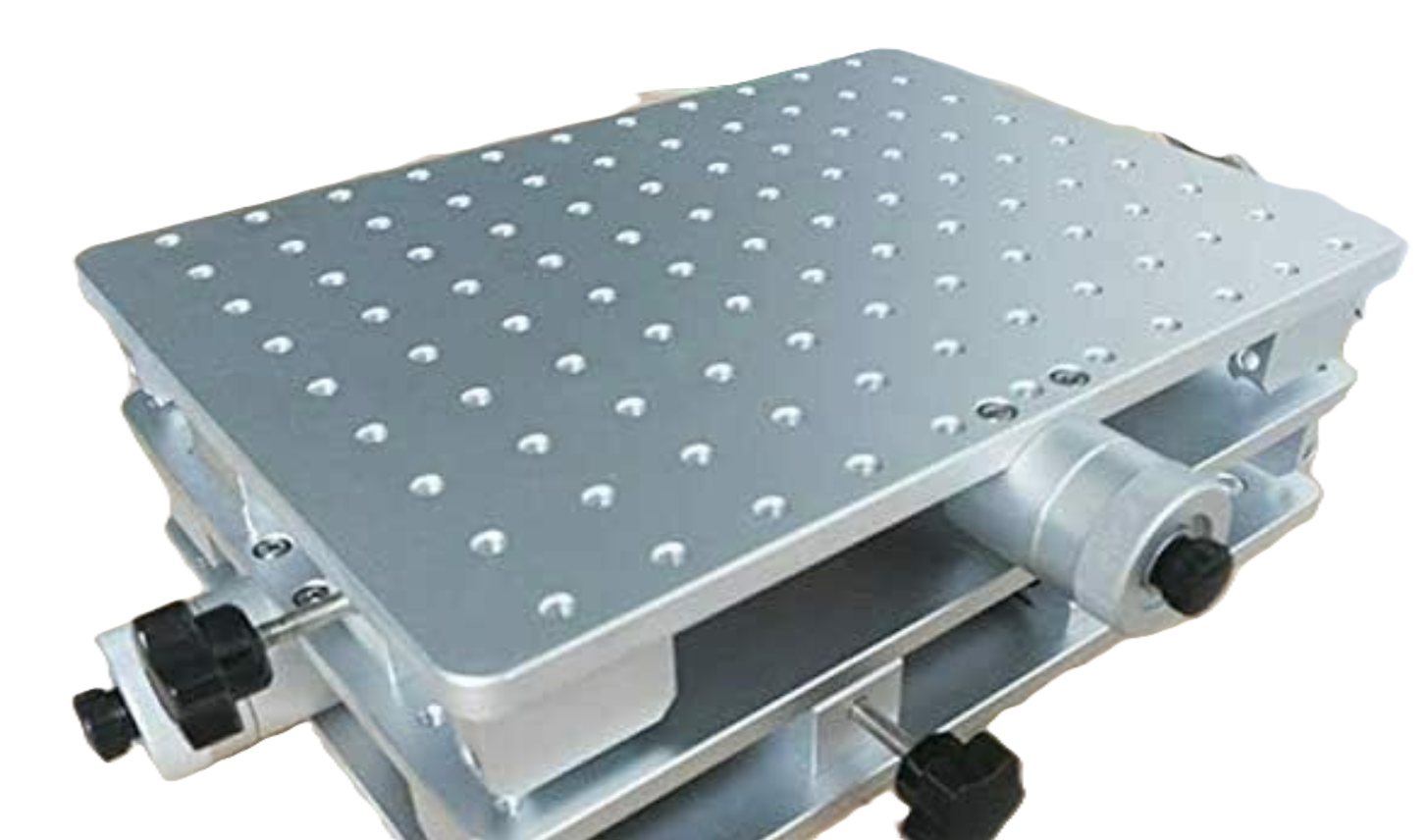
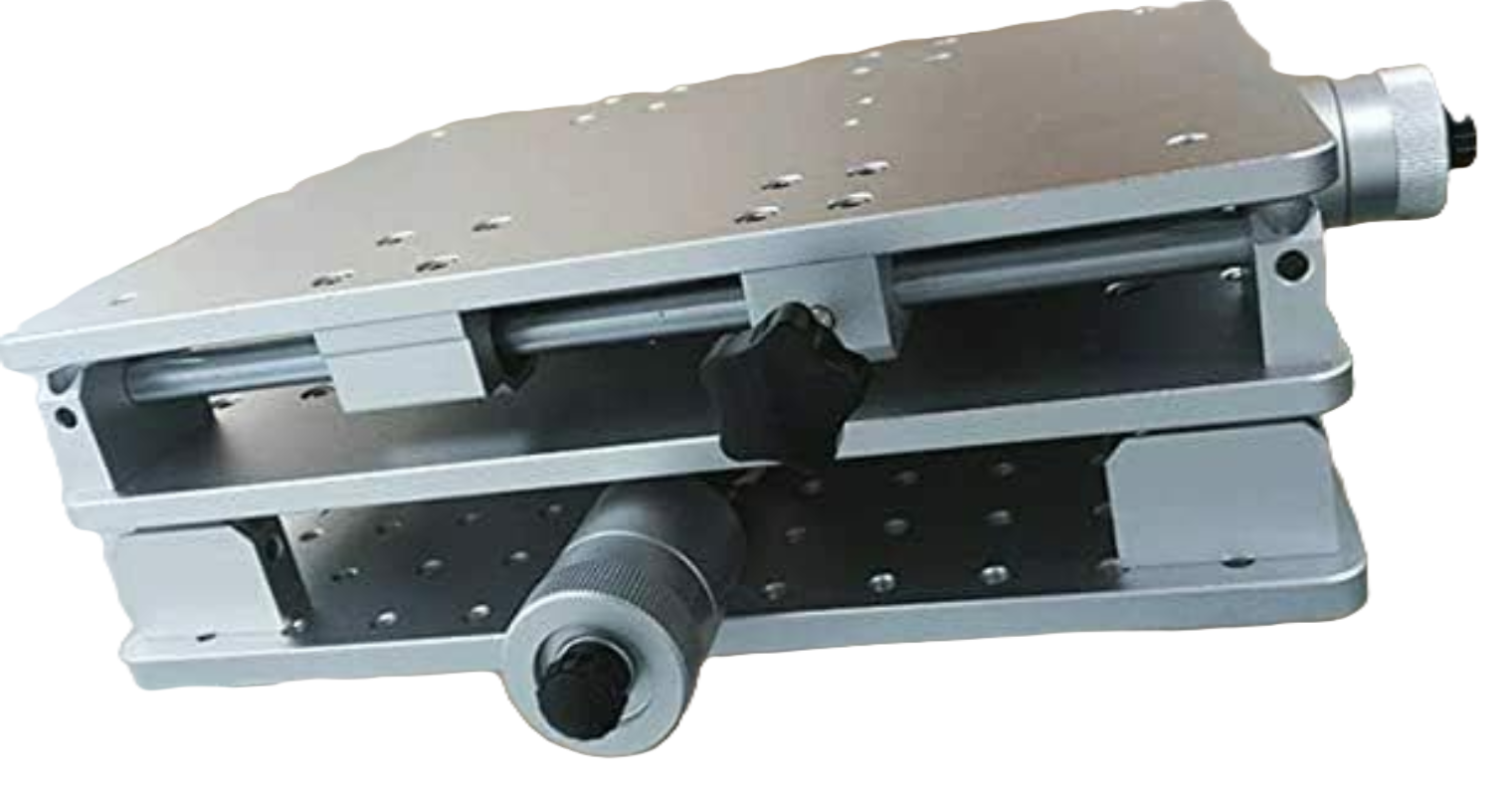
2D worktable or flatbed
A 2D table, also known as a 2D worktable or flatbed, is a fundamental component of laser marking machines, providing a stable and precise surface for material processing. It plays a crucial role in ensuring accurate marking and engraving on various materials.
Key Features of 2D Tables for Laser Marking Machines:
Material Composition: Typically constructed from high-quality, heat-resistant materials such as stainless steel or aluminum to withstand the thermal effects of laser processing.
Design: Often features a flat, perforated, or honeycomb surface to facilitate efficient gas flow and debris removal during the marking process.
Size and Compatibility: Available in various sizes to accommodate different machine models and material dimensions.
Adjustability: Some 2D tables offer adjustable height and tilt functions to accommodate materials of varying thicknesses and to achieve optimal marking angles.
Benefits:
Enhanced Precision: Provides a stable and level surface, contributing to accurate and consistent marking results.
Improved Efficiency: Facilitates optimal gas flow and debris removal, reducing the risk of material contamination and improving processing efficiency.
Extended Equipment Life: Protects the underlying machine components from heat damage and debris, potentially extending the lifespan of the laser system.
Applications:
Metal Processing: Ideal for marking and engraving metals such as carbon steel, stainless steel, aluminum, and brass.
Non-Metal Processing: Suitable for processing non-metal materials like plastics and composites, depending on the machine's capabilities.
A 2D table, also known as a 2D worktable or flatbed, is a fundamental component of laser marking machines, providing a stable and precise surface for material processing. It plays a crucial role in ensuring accurate marking and engraving on various materials.
Key Features of 2D Tables for Laser Marking Machines:
Material Composition: Typically constructed from high-quality, heat-resistant materials such as stainless steel or aluminum to withstand the thermal effects of laser processing.
Design: Often features a flat, perforated, or honeycomb surface to facilitate efficient gas flow and debris removal during the marking process.
Size and Compatibility: Available in various sizes to accommodate different machine models and material dimensions.
Adjustability: Some 2D tables offer adjustable height and tilt functions to accommodate materials of varying thicknesses and to achieve optimal marking angles.
Benefits:
Enhanced Precision: Provides a stable and level surface, contributing to accurate and consistent marking results.
Improved Efficiency: Facilitates optimal gas flow and debris removal, reducing the risk of material contamination and improving processing efficiency.
Extended Equipment Life: Protects the underlying machine components from heat damage and debris, potentially extending the lifespan of the laser system.
Applications:
Metal Processing: Ideal for marking and engraving metals such as carbon steel, stainless steel, aluminum, and brass.
Non-Metal Processing: Suitable for processing non-metal materials like plastics and composites, depending on the machine's capabilities.
A 2D table, also known as a 2D worktable or flatbed, is a fundamental component of laser marking machines, providing a stable and precise surface for material processing. It plays a crucial role in ensuring accurate marking and engraving on various materials.
Key Features of 2D Tables for Laser Marking Machines:
Material Composition: Typically constructed from high-quality, heat-resistant materials such as stainless steel or aluminum to withstand the thermal effects of laser processing.
Design: Often features a flat, perforated, or honeycomb surface to facilitate efficient gas flow and debris removal during the marking process.
Size and Compatibility: Available in various sizes to accommodate different machine models and material dimensions.
Adjustability: Some 2D tables offer adjustable height and tilt functions to accommodate materials of varying thicknesses and to achieve optimal marking angles.
Benefits:
Enhanced Precision: Provides a stable and level surface, contributing to accurate and consistent marking results.
Improved Efficiency: Facilitates optimal gas flow and debris removal, reducing the risk of material contamination and improving processing efficiency.
Extended Equipment Life: Protects the underlying machine components from heat damage and debris, potentially extending the lifespan of the laser system.
Applications:
Metal Processing: Ideal for marking and engraving metals such as carbon steel, stainless steel, aluminum, and brass.
Non-Metal Processing: Suitable for processing non-metal materials like plastics and composites, depending on the machine's capabilities.